Dipole Rotation Approach
TDR Cure Monitoring provides a signal from small, embedded electrode sensors. The location of
significant cure events are identified, such as viscosity minimum, gel point, and end of cure. The information is
used in designing process control and optimization for active autoclave control. The TDR system is straightforward
to integrate and provides a new high level of performance compared to conventional dielectric sensing.
TDR Cure Monitoring relies exclusively on rotating polar molecules called dipoles.
Rotating dipoles are a better indicator of absolute cure, since their chemistry and concentration is well-known.
The dipole spectrum provides a unique signature, detailing viscosity, percent cure, and degree of sensor contact.
Results are quantitative and reproducible, and not based on poorly-characterized conducting ions.
Rotating dipoles have an intrinsic molecular dynamics independent of sensor configuration.
Conducting ions have no internal dynamics other than charging effects at the electrode. Rotating dipoles thus
provide molecular-level information which can be used to deduce individual cure parameters.
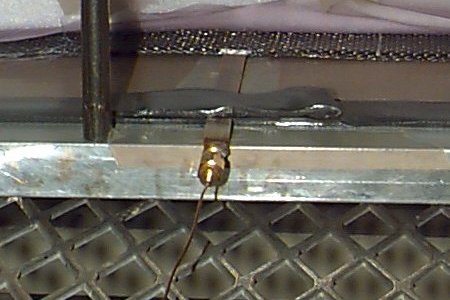
Frequency-Domain Cure Monitoring
In Frequency-Domain Cure Monitoring, the reflected pulse is transformed to the
frequency domain and displayed as a dipole relaxation spectrum. Results are displayed as a complex storage
and loss modulus, similar to mechanical rheological measurement. Changes occurring in loss modulus for
Hexcel 8552 during 125°C isothermal cure are seen in the sequence below.
The frequency of the dipole loss peak is related to viscosity through the
Debye Model of Viscous Rotation. The specific frequency-viscosity relationship is initially calibrated
using simultaneous TDR and rheometry measurement; subsequent runs then use this calibration to predict
viscosity based on loss peak frequency. Typical results for Hexcel 8552 are shown below.
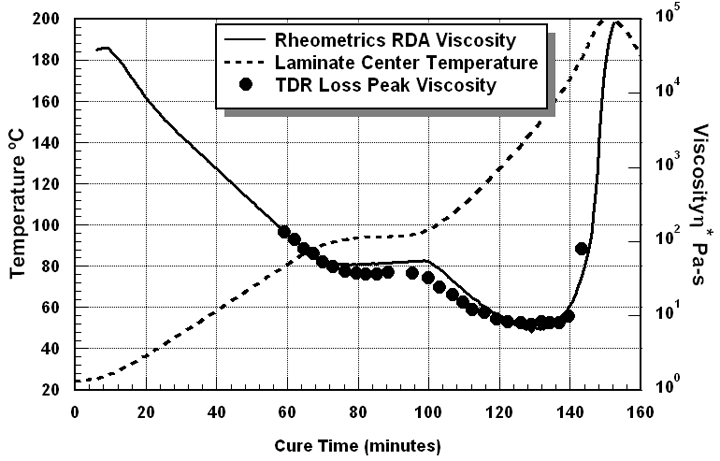
Time-Domain Cure Monitoring
The same features are seen in the direct reflected pulse,
from which the frequency data is derived. From Fourier analysis, high frequency signals in
the frequency domain are concentrated at short times in the time domain; low frequency signals
in the frequency domain are concentrated at long times in the time domain. A shift in reflected
pulse amplitude from long to short times in the time domain thus mirrors a shift in transition
frequency from low to high frequencies in the frequency domain, and vice-versa. This forms the
basis for time-domain TDR cure monitoring.
When the reflected pulse amplitude at 1 ns is plotted as a function of
cure time it qualitatively mirrors the viscosity data. It also tracks during the entire cure
cycle, even when the loss peak frequency is below the field of view. The 1 ns amplitude thus
provides a “window” on a high-frequency component of the changing dipole spectrum (~1GHz)
and rises and falls as the spectrum slides in and out of this window. The measurement provides
a simple and robust measurement of high-frequency dynamic response.
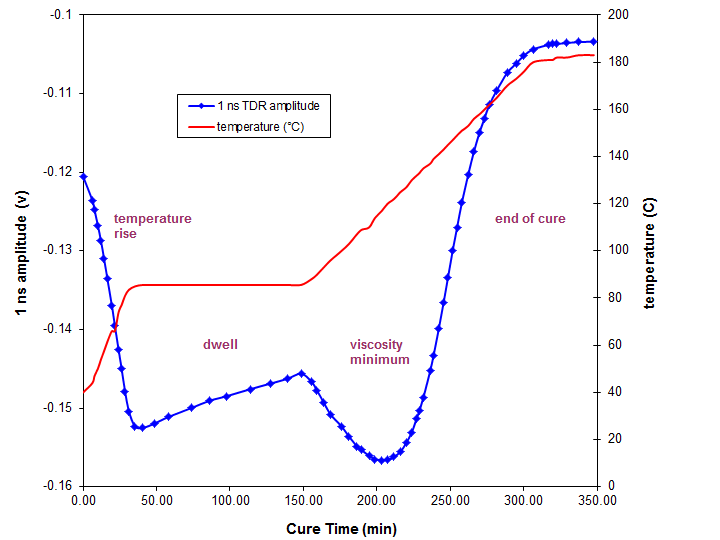
The reflected pulse amplitude at other delays provides additional
information. The amplitude at 50 ns monitors a low frequency component in the changing dipole
spectrum (~20 MHz) such that the bulk of the spectrum must pass through this range on its way
from low to high frequencies. As it passes through the signal reverses, since the spectrum is
now moving away, rather than toward, the field of view. This reversal provides a unique signature,
at both the beginning and end of viscosity profile, which can be used to interpret viscosity at
points other than the viscosity minimum.
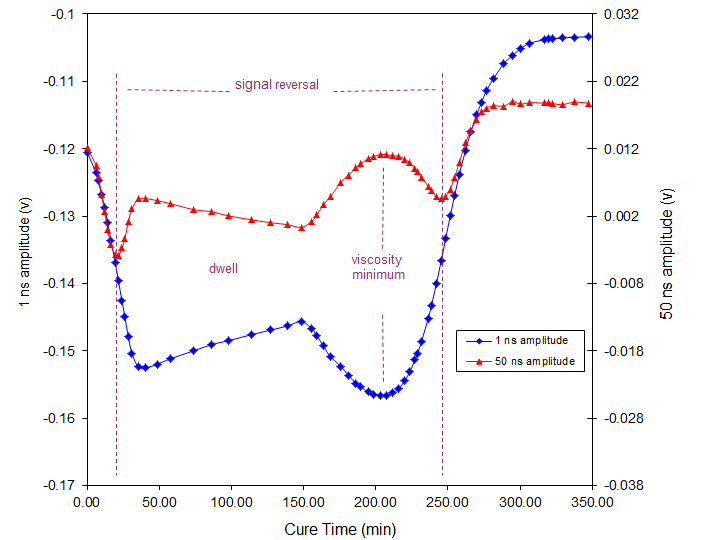
Planar Capacitance Sensors
TDR Cure Monitoring has a clear advantage because of the simplicity
of the sensing transducers. Electrode sensors are versatile, inexpensive, and tolerant of
hostile environments. They can be unobtrusively embedded in the process material and left
in place after use. Unlike mechanical transducers they cover wide ranges in frequency with
a single geometry.
TDR cure sensors are small because of the high operating frequency.
A small low-capacitance electrode becomes an efficient capacitance sensor when operating at
TDR frequencies of 100 MHz and above. A small sensor size is critical in minimizing intrusion
into the process material.
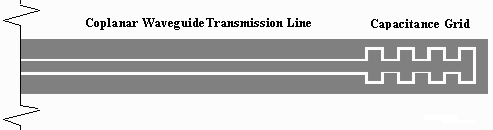
TDR planar strip sensors keep sensor intrusion to a minimum.
Available in thickness' of 0.25 mm and 0.125 mm, TDR strip sensors can be custom-
engineered to a variety of lengths and widths. The sensing area is typically 5 mm wide,
with a 3 mm transmission path leading to the sensor. The sensor can either be trimmed
to these dimensions, or used as part of a wider strip.
TDR Cure Monitoring has an additional advantage. Because the
traveling pulse is localized, the line leading to the sensor can also be used for
time-of-flight fault testing when cure is complete. This can be useful in detecting
flaws and damage in the finished material in-service.
Technical References
Additional information on TDR Composite Cure Monitoring can be found at:
-
High-Performance Composites Magazine, September 2006
http://www.compositesworld.com/articles/monitoring-the-cure-itself
-
N.E. Hager III, R.C. Domszy, "Time-Domain-Reflectometry Cure Monitoring",
SAMPE Proceedings Long Beach CA, 2001 May 6-10, p. 2252. [downloadable pdf format:,
pubs/msi_composite_sampe_2001.pdf
-
N.E. Hager III, R.C. Domszy, "Time-Domain-Reflectometry Cure Monitoring", American Helicopter Society -
Affordable Composite Structures Proceedings, Briegeport CT, Oct 1998.
-
N.E. Hager III, R.C. Domszy, U. S. Patent 5,872,447 (1999).
-
S. Carrozzino, G. Levita, P. Rolla, E. Tombari, Poymer Engr. & Sci. 30, 366 (1990).
-
A. Liva, G. Levita, P. A. Rolla, J. Appl. Polymer Science, 50, 1583 (1993).
-
E. Marad, K. R. Baker, J. D. Graybeal, Macromolecules, 25, 2243 (1992).
.
Copyright © 2015 Material Sensing & Instrumentation, Inc.

|